All buildings are surrounded more or less by natural moisture. Most buildings also contain moisture produced internally by normal habitation. Therefore, appropriate design measures are essential to keep the moisture away from the buildings. When these measures are insufficient, dampness can enter the building materials and cause deterioration.
Rising Damp
Mechanism of Attack – Rising dampness is concerned with the movement of water from the ground to the porous material of the walls. It commonly happens in walls near the ground level and solid ground floor slabs, mainly at junctions with the walls.
The moisture movement through the porous material takes place in saturated, as well as unsaturated soils.
Saturated soil has its interstitial spaces filled with water. This usually saturates a porous material in contact due to hydrostatic pressure, permitting water to flow into the pores.
Unsaturated soils also contain water held around the points of contact by surface tension. Water is drawn into the pores of the material by capillary action in the latter case. After entering the base of a wall, the water will move up mainly by capillarity. The height of the rise of moisture depends on the pore structure of the wall, the degree of saturation of the soil, and the rate of evaporation.
Groundwater invariably contains dissolved hygroscopic salts which crystallize out on the wall surface where the water evaporates. When the air is humid, these salts will attract moisture from the laden air to cause apparent ‘dampness’ on the wall.
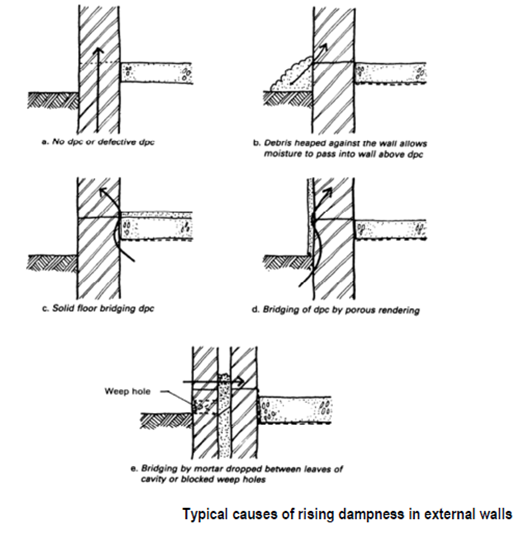
Causes of Rising Damp – Defective Damp Proof Courses (DPC) and poor detailing where such courses are provided constitute the main causes of rising dampness (see figure above).
Examples include the following:
- Absence of DPC in very old buildings.
- Bridging of DPC internally by a floor screed being laid without a membrane or including a membrane that is not keyed or chased into the DPC in the wall.
- Bridging of DPC by an external rendering which is likely to crack and allow moisture to rise in the gap formed behind it.
- Bridging by earth deposited against the outside of the wall.
- Bridging caused by mortar droppings and other debris into the void of the cavity wall construction.
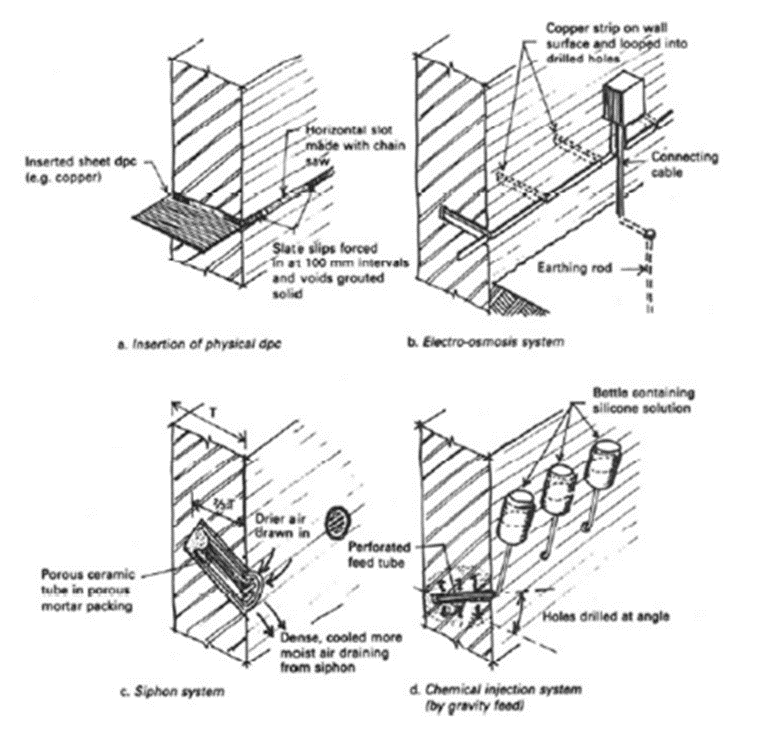
Remedial Measures – Some causes of rising dampness can be dealt with economically and easily (see figure above). For example, it may be possible to lower earth or paving that extends above the DPC, or to remove rendering or pointing which bridges the DPC.
Where there is no DPC or where it is defective, more expensive methods involving either installing a new DPC in situ, or removing the cause of the bridging by conventional building methods are necessary.
1 Physical Insertion of DPC – An early method is cutting out one or two courses of bricks to the full thickness of the wall at the appropriate level and then building it with new engineering bricks. New techniques involve removing a horizontal mortar joint by cutting through the full thickness of the wall, using a tungsten carbide tipped saw, for lengths of about 1.200 m at a time. Various damp-proof materials can be used, including copper, bituminous felt, or polyethylene. It is necessary to overlap all joints by at least 150 mm and the space above the DPC is usually made good and solid with cement mortar.
2 Installation of Siphons – In this method, siphons in the form of porous clay ceramic tubes are inserted into holes in the affected walls. These tubes are held in position by a salt-free porous mortar packing. The holes are then covered with a ventilator. The technique depends on rising dampness being drawn into the siphon tubes by capillarity. The tube is designed and positioned to discharge the humid air developed inside it and replace it with fresh air. One major disadvantage of this technique is that the pores on the surface of the tube can become blocked by the accumulation of salts during the evaporation process.
3 Chemical Injections – The main types of chemicals used for injection fluids are Silicones, Siliconates, or Stearates. Application is either by pressure injection or by a diffusion technique based on gravity. In the pressure injection method, an aqueous solution of Siliconates, such as Sodium or Potassium Methyl Silicone, is pumped into predrilled holes at about 150 mm centers, usually along the mortar joint. Injection is done by a lance designed to maintain constant pressure during the process. The volume of fluid to be injected will depend on the thickness of the wall and the type of material. The gravity-feed system requires a series of holes to be drilled at a downward-sloping angle at the position of the new damp-proof course. The diffusion liquid is applied from a container that feeds the tube by gravity. The fluid must diffuse into the wall completely to be effective. Sufficient time must be provided for all fluid to flow from the container and to be absorbed by the wall, which may take up to a few days.
Other Treatments
1 Re-plastering – The hygroscopic salts deposited on wall surfaces with the evaporation of water continue to absorb moisture from the atmosphere even after the rising dampness has been eliminated. Therefore, for any treatment to be completely satisfactory the old salt-contaminated plaster must be removed and a new plaster applied. A cement-based plaster of 3:1 sand/cement mix should be used. The protection can be further enhanced by incorporating waterproof additives such as stearates or styrene butadiene in the mix.
Rain Penetration
Effects of Rain Penetration – Rainwater is the obvious and common reason for dampness. Its penetration through external walls and roofs may take place due to gravity flow, wind forces, and capillary action in the pores of the materials.
Rain penetration has the following effects which tend to lead to failure:
- Loss of adhesion and/or cracking of finishes due to chemical reaction with elements of the background material.
- Cracking of components or elements due to moisture movement during wetting or drying out; and chemical reactions such as reinforcement corrosion.
- Changes in the appearance of the surface such as staining.
Causes of Rain Penetration – External walls should be sufficiently thick to absorb rainwater and allow it to evaporate later or be constructed as cavity walls to break the capillary flow of moisture towards the interior. Other measures may include wide overhanging eaves at roof level and the use of impervious membranes for roof construction.
The principal causes of rain penetration can be summarized as follows:
- The permeability of porous materials, particularly clay bricks and lightweight concrete used for wall construction, allows some absorption of water.
- Inadequate provision for drainage arising from under-designed gutters and downpipes, and poor maintenance.
Contributory factors to Rain Penetration – The amount of rainwater that can penetrate into or through an element such as a wall or roof depends on the exposure of the element to rain, the water-excluding characteristics of the units, components, and joints making up the construction of the element, and the modes of transmission of the water within the thickness of the construction of the element.
1 Exposure – The possibility of rain penetration, particularly through vertical surfaces, depends on both the quantity of rainfall and wind speed. The angle at which rain strikes a wall depends on wind speed and raindrop size. The bigger the size of raindrops, the greater will be the wind speed required to induce the angle of incidence of raindrops on a wall. Otherwise, the raindrops will fall vertically. A direct relationship, therefore, exists between the amount of rain that falls on a wall surface and the degree of exposure of the site. Buildings located on more exposed sites, such as those on elevated ground, are more vulnerable to penetrating dampness caused by driving rain.
2 Water-excluding Characteristics – The extent of rain penetration also depends on the water-excluding characteristics of the materials used for the element. With the use of permeable materials in walls, for example, there is a higher risk of rain penetration.
3 Modes of Transmission – There are three main modes of water transmission through an element as a whole which can affect the amount of rainwater penetrating into the building. The upward rise of water is entirely by capillarity through the pores of porous materials or along fine cracks at the interface of units of components.
Rain Penetration through Cavity Walls – If constructed properly, the cavity wall is most effective in the prevention of rainwater penetration. Although the outer leaf of the walls may suffer a high degree of water penetration, the cavity can prevent rainwater from going into the inner leaf. Any mortar which inevitably falls on the wall ties and cavity trays must be removed. Ties should not be fixed with a slope from the outer to the inner leaf.
Procedure to rectify water penetration in a cavity wall
1 Repointing – If the existing mortar is deteriorating and eroding, then repointing is most likely to be effective. It can be an expensive measure since it may be necessary to chase out existing joints. Raked joints are sometimes linked with penetration problems in exposed walls. These joints can be filled to the front surface of the wall and perhaps finished with a weather-struck joint. It may also be necessary to re-point before applying water repellents, sealants, or paints.
2 Water Repellents – Colourless waterproofing solutions based on 5 percent silicone or aqueous siliconates can be used on porous walls. The major effect of water repellents is to reduce rainwater absorption.
3 Sealants – There are several sealants available, most of them being based on acrylic polymers. They are more visible than water repellents since they form a film on the surface which can give it a glazed appearance. Sealants act by blocking the pores of the bricks and so will restrain the movement of water vapour through the surface.
4 Masonry Paints – There is a wide range of paint types available for a masonry which will seal the surface in much the same way as colourless acrylics but will usually be able to seal the cracks effectively by filling them. Examples include cement paints and other emulsified formulations incorporating acrylic resins, bitumens, PVA, or styrenes. These paints provide relatively porous coatings so that, while rainwater penetration may be reduced, evaporation of water vapour and drying out can continue, although at a reduced rate. A disadvantage is that the paint may not be aesthetically acceptable because of the change in colour of the wall. Paints are also generally more expensive than water repellents.
5 Cladding – A cladding in the form of slates, sheet metal, or tiles hung vertically on the wall can provide useful protection against penetrating dampness. The tiles, with moisture-resisting backing, should be fitted to preservative-treated battens using suitably protected nails.
Condensation
Mechanism of Condensation – Air is said to be saturated when it holds the maximum amount of moisture that it can contain at that temperature. When air that is not saturated is cooled, it reaches a temperature called the dew point at which it can be saturated. Any further cooling of the air below the dew point will result in the precipitation of liquid water as condensation. In tropical climates, materials rarely attain a low enough temperature to get below the dew point. When this condition does happen, it is often due to cold temperatures being created within an air-conditioned building, with resulting condensation appearing on the outside of the building enclosure. In moderate climates, however, hot and cold air temperatures are reversed and the problem of condensation inside a building becomes more serious.
Effect of Condensation – One of the inevitable consequences of condensation is the formation of growths of fungi and bacteria. These growths increase on surfaces in buildings once the humidity rises above 70 percent relative humidity, producing and liberating microorganisms that are responsible for the characteristic black, green, and white colours.
Proprietary fungicidal washes can be used on surfaces where persistent growth occurs. If decorative finishes are badly affected or damaged, they are best removed first.
Controlling Condensation – Various measures are available to reduce the problem of condensation in buildings, including ventilation.
Ventilation – In all cases of condensation, adequate ventilation is required to remove the humid air from the building. The best way is to use an extractor fan in a humid room such as the kitchen or bathroom. Some extractors are controlled by sensors which operate only when the humidity levels rise.
Other Sources of Dampness
Entrapped Moisture During Construction – In structures that are constructed in situ, as opposed to being of precast or prefabricated construction, the water content can represent a high proportion of the weight of materials. If sufficient time is not provided to permit this water to dry out, particularly when there is a need to speed up the construction process, dampness may take place in the structure.
Faulty Plumbing and Rainwater Discharge Systems – Plumbing systems in a building need attention to make sure that joints are tight and all metallic fittings are protected against corrosion by regular preventive maintenance. Internal damp conditions may be accelerated with faulty plumbing systems that are concealed in walls and floors. Gutters and downpipes used to discharge rainwater from the roof of a building must be correctly designed to prevent overflowing. Metallic parts may be affected by corrosion arising from atmospheric pollution or by contaminated water. Regular maintenance to clear any blockage by fallen leaves and other debris is also vital.
Moisture from Occupation of Buildings – Moisture comes from cleaning, washing, and cooling activities inside the building. Floors should be designed to slope towards gullies in kitchens, bathrooms, toilets, and laboratories. In these cases, the floor finishes should be resistant to constant wetting. Any leak occurring through defective floors and drains can cause internal dampness in the structure below.