The term cement refers to materials that act as adhesives. However, in this context, its use is restricted to that of a binding agent for sand, stone, and other aggregates within the manufacture of mortar and concrete.
Hydraulic cement sets and hardens by internal chemical reactions when mixed with water.
Non-hydraulic materials such as lime will only harden slowly by absorption of carbon dioxide from the air.
Lime was used throughout the world by ancient civilizations as a binding agent for brick and stone. The concept was brought to Britain in the first century AD by the Romans, who used the material to produce lime mortar. Romans frequently mixed lime with volcanic ashes, such as pozzolana, to convert a non-hydraulic lime into hydraulic cement. They used it for constructing aqueducts and other buildings.
LIME – as a construction material in Sri Lanka
There is a long history of production and use of lime in Sri Lanka. It was mainly used as a cementing agent and also as a decorative whitewash in the building industry. The use of lime as a building material dates back to the Anuradhapura and Polonnaruwa periods. The famous gallery of Sigiriya known as “Kadapath paura” had been coated with lime plaster. It was polished so well that even today, it shines like glass.
In recent years, the demand for lime has increased in other areas. It is now used for water treatment works, in the sugar industry, and also for agricultural purposes. There are other miscellaneous applications such as earth stabilization works in road construction.
Traditional methods of lime production are still used in Sri Lanka. However, few efforts have been made to improve upon these methods, mainly by improving the kiln design.
Coral and shell deposits, the raw materials traditionally used for lime production, are mainly confined to the southwestern and southern coastal belts of Sri Lanka.
In the central hill country, lime is produced by making use of dolomite deposits. Dolomite is a type of limestone containing a proportion of magnesium carbonate (MgCO3) as well as calcium carbonate (CaCO3).
Manufacture of Lime
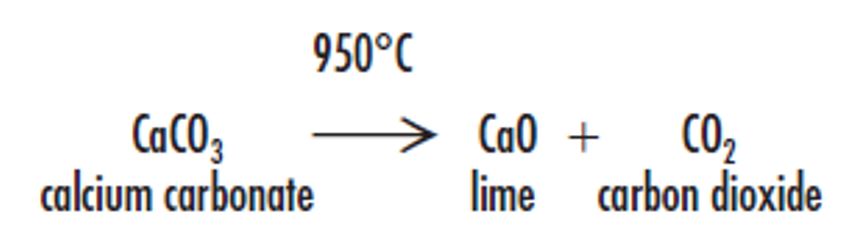
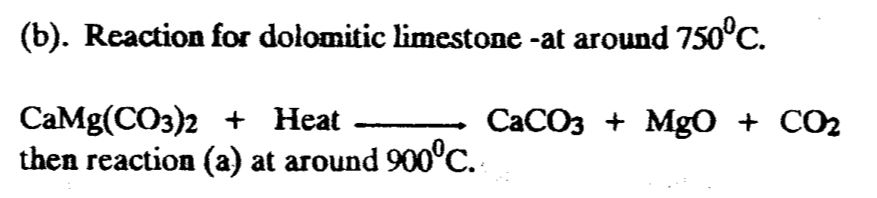
Lime is manufactured by calcining natural calcium carbonate, typically hard-rock carboniferous limestone. The mineral is quarried, crushed, ground, washed, and screened to the required size range. The limestone is burnt at approximately 950°C in either horizontal rotary kilns or vertical shaft kilns which drive off the carbon dioxide to produce quicklime or lump lime (calcium oxide).
In Sri Lanka limestone occurs in various forms, which include:
- Miocene limestone (over 95% CaCO3)
- Coral (over 95% CaCO3)
- Shell (over 95% CaCO3)
- Dolomite (MgO (variable 8% -21%))
- Calcite (CaCO3 (100% pure))
Miocene limestone is mostly used for the manufacturing of hydraulic cement. Calcite is limited in its occurrence. It is used in the ceramic industry. Shell, coral, and dolomite are used for lime production. However, coral and shell deposits will likely be exhausted within the next 8 to 10 year time. Therefore, Dolomite deposits and the Miocene limestone would finally have to be the raw materials for lime manufacture.
Coral and shell occur in the size range which can be directly used in kilns. Dolomite, which is used in the hill country, is readily accessible. But it needs to be quarried and broken down into lumps of the required size. It is extracted manually using crowbars, picks, and hammers. Large boulders are blasted by using dynamite. The dolomite is then broken down by hammer to a kiln feed size of 50-80 mm diameter.
The kiln and firing methods
The main type of firewood used is the trunk of the coconut palm cut into lengths of about 75 cm. Coconut palm leaves, husks, and coconut shells are normally used to start the fire in the kiln.
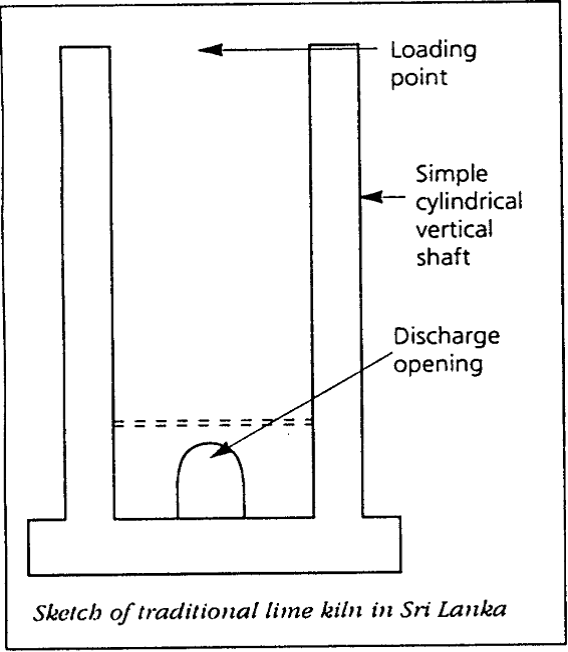
A typical kiln in a coastal area has a cylindrical inner wall that ranges in diameter from about 1 to 1.5 meters. The height ranges from 2.5 to 3.0 meters. The kiln is constructed with normal cottage-type clay engineering bricks set in a lime clay mortar. The firing openings are at the bottom of the kiln. The kiln is charged with alternate layers of fuelwood and limestone (coral). At the base are placed fuelwood and other materials to rapidly initiate a fire.
For each batch, about 1.5 to 3 tons of coral are used together with around 0.75 to 1.5 tons of fuelwood. The kiln is ignited and allowed to burn for approximately 48 hours and then cooled to recover about 0.75 to 1.5 tons of quicklime (CaO). Discharging is carried out from the bottom. Batch-type kilns are normally used to burn coral and shell. Depending on capacity, the output of the kilns varies considerably.
In the hill country, with dolomite as the raw material, kilns are of the continuous type and are taller than the kilns in the coastal area. They are 3.0 to 3.5 meters high with an inner diameter of 1 to 1.5 meters. About 2 tons of dolomite is loaded into these kilns alternating with fuelwood (coconut palm trunks), and daily a ton of quicklime is recovered from the bottom with stone and fuelwood continuously being replenished at the top.
Slaking of lime
(Hydration of quicklime)
Most of the quicklime taken from the kiln is of reasonable particle size for hydration. In any case, there is a fair amount of air slaking before the actual slaking operation is carried out, which is done by pouring water over a fairly large pile of quicklime which is then mixed manually with a shovel. The hydrated lime is then sieved to remove the larger lumps of lime which have not hydrated properly before the product is bagged.
No milling is undertaken because the building industry and other users of lime are satisfied with the product in this state, and to keep the processing costs low. The average calcium oxide content by mass in lime samples from the coastal area is 58 percent and in dolomitic lime samples 43 percent. The magnesium oxide content by mass in the hill country dolomitic samples of lime is around 26 percent.
Mode of operation
Production in the coastal area is on a batch basis with the recovery of about a ton of lime each day. Kilns are fired depending on the availability of coral, which is getting scarcer each day. Lime is normally sold by ton, although units of 50 kg and 25 kg are also available.
With the production of dolomitic lime, it should be noted that in dolomite the magnesium carbonate (MgCO3) components dissociates to magnesium oxide (MgO) at around 775°C. The dolomite when heated to 900°C, the lowest temperature normally used to break down the calcium carbonate (CaCO3) component to calcium oxide (CaO), will produce MgO which is over-burnt and not readily converted to the hydroxide, Mg(OH)2. If this material is used without allowing the hydration to be completed, blistering of plasters can occur if used for plastering walls. If the dolomite lime is to be used for mortar it need only be kept for about three days after slaking. Masons and plasterers claim that dolomitic lime should be added to water and not water to dolomitic lime for satisfactory results and kept for as long a period as possible.
Slaking
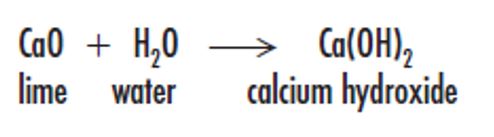
Slaking is the addition of water to quicklime which is a highly exothermic reaction. The controlled addition of water to quicklime produces hydrated lime (mainly calcium hydroxide) as a dry powder. It is suitable for use within mortars or in the manufacture of certain aerated concrete blocks. Generally, the addition of lime to cement mortar, render or plaster increases its water-retention properties, thus retaining workability, particularly when the material is applied to absorbent substrates such as porous brick. Lime also increases the cohesion of mortar mixes allowing them to spread more easily. Lime-based mortars remain sufficiently flexible to allow movement but additionally, due to the presence of uncarbonated lime, any minor cracks are subsequently healed by the action of rainwater. Hydrated lime absorbs moisture and carbon dioxide from the air, and should therefore be stored in a cool, draught-free building and used whilst still fresh.
Lime putty
Lime putty is produced by slaking quicklime with an excess of water for several weeks until a creamy texture is produced. Alternatively, it can be made by stirring hydrated lime into the water, followed by conditioning for at least 24 hours. However, the traditional direct slaking of quicklime produces finer particle sizes in the slurry; the best lime putty is produced by maturing it for at least six months.
Lime putty may be blended with Portland cement in mortars where its water-retention properties are greater than that afforded by hydrated lime. Additionally, lime putty, often mixed with sand to form coarse stuff, is used directly as a pure lime mortar, particularly in restoration and conservation work. It sets, not by reaction with sand and water, but only by carbonation, and is therefore described as non-hydraulic. Limewash, as a traditional surface coating, is made by the addition of sufficient water to lime putty to produce a thin creamy consistency.
Carbonation
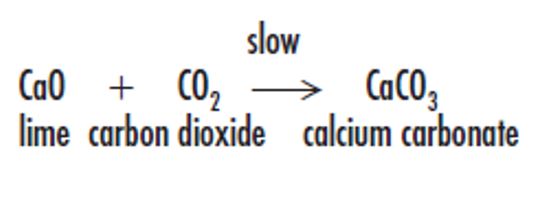
Lime hardens by the absorption of carbon dioxide from the air. Then, it gradually reconverts the calcium oxide back to calcium carbonate. The carbonation process is slow, being controlled by the diffusion of carbon dioxide into the bulk of the material. When sand or stone dust aggregate is added to the lime putty to form a mortar or render, the increased porosity allows greater access to carbon dioxide and a speedier carbonation process. The maximum size of aggregate mixed into lime mortars should not exceed half the mortar-joint width. Typical lime mortar mixes are within the range of 1:2½ and 1:3, lime putty: aggregate ratio. Because of the slow carbonation process, masonry lifts are limited, and the mortar must be allowed some setting time to prevent its expulsion from the joints.
Love your article on usage of lime and its construction characteristics
Thank you very much!