GLASS
The term glass refers to materials, usually blends of metallic oxides, mainly silica, which do not crystallize when cooled from the liquid to the solid state. It is the non-crystalline or amorphous structure of glass that gives rise to its transparency.
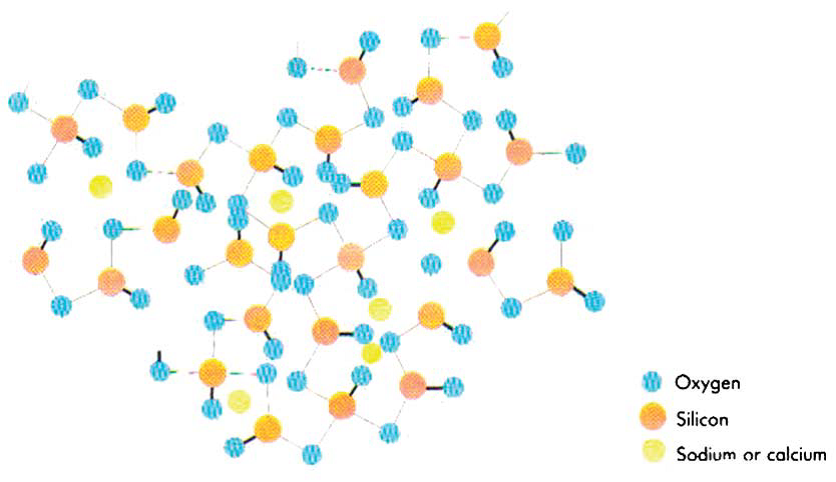
Glass made from sand, lime, and soda ash has been known in Egypt for 5000 years. For many centuries glass was worked by drawing the molten material from a furnace. The glass was then rolled out or pressed into appropriate moulds and finally shaped by cutting and grinding.
Adding different metallic compounds to the melt, various coloured glasses can be manufactured. The blue colour was obtained by the addition of cobalt. Copper gives blue or red and iron or chromium produced green. In the fifteenth century, white opaque glass was produced by the addition of tin or arsenic. In the seventeenth century, ruby-red glass was made with the addition of gold chloride. Clear glass could be obtained by using antimony or manganese as a de-colourizer. These remove the green colouration caused by iron impurities within the sand.
In the late twentieth century, with the advent of fully glazed facades, the construction industry has become a major consumer of new glass.
MANUFACTURE
Soda lime silicate glass
Modern glass is manufactured from sand (silica), soda ash (sodium carbonate), and limestone (calcium carbonate). Small additions of salt cake (calcium sulfate) and dolomite (magnesium limestone) are also used. This gives a final composition of typically 70–74% silica, 12–16% sodium oxide, 5–12% calcium oxide, and 2–5% magnesium oxide with small quantities of aluminium, iron, and potassium oxides. The addition of 25% broken glass or cullet to the furnace mix accelerates the melting process. It also recycles the production waste. The production process is relatively energy intensive at 15,000 kWh/m3.
Alkaline earth silicate, borosilicate, and ceramic glass
Alkaline earth silicate and borosilicate glasses are also used in the construction field. These have considerably different chemical compositions, and, give their particular physical properties. The composition of alkaline earth silicate glass is typically 55–70% silica, 5–14% potassium oxide, 3–12% calcium oxide, and 0–15% aluminium oxide, with small quantities of zirconium, strontium, and barium oxides.
Borosilicate glass is typically 70–87% silica, 0–8% sodium oxide, 0–8% potassium oxide, 7–15% boron oxide, and 0–8% aluminium oxide, with small quantities of other oxides. A particular characteristic of borosilicate glass is that it has a coefficient of expansion of one-third that of standard soda lime silicate glass. This property makes it considerably more resistant to thermal shock in case of fire.
Glass-ceramics have a zero coefficient of expansion. It makes them highly resistant to thermal shock. The composition of glass ceramics is complex comprising typically 50–80% silica, and 15–27% alumina, with small quantities of sodium oxide, potassium oxide, barium oxide, calcium oxide, magnesium oxide, titanium oxide, zirconium oxide, zinc oxide, lithium oxide, and other minor constituents.
The glass is initially produced by a standard float or rolling technique, but subsequent heat treatment converts part of the normal glassy phase into a fine-grained crystalline form, giving rise to particular physical properties.
FORMING PROCESSES
Early methods
Initially, crown glass was formed by spinning a 4 kg cylindrical gob of molten glass on the end of a blowpipe. The solid glass was blown, flattened out, and then transferred to a solid iron rod. After reheating it was spun until it opened out into a 1.5 m diameter disc. The process involved considerable wastage including the bullion in the center.
An alternative process involved the blowing of a glass cylinder which was then split open and flattened out in a kiln. Subsequently, in a major development, circular metal bait was lowered into a pot of molten glass and withdrawn slowly. It drags up a cylindrical ribbon of glass 13 m high. The diameter of the cylinder is maintained with compressed air. The completed cylinder was then detached, opened up, and flattened out to produce flat window glass.
With the development of the Fourcault process in Belgium and the Colburn process in America that it became possible to produce flat glass directly. A straight bait was drawn vertically out of the molten glass to produce a ribbon of glass, which was then drawn directly up a tower, or in the Colburn process turned horizontally, through a series of rollers; finally, appropriate lengths were cut off. However, such drawn sheet glass suffered from manufacturing distortions. This problem was overcome by the production of plate glass, which involved horizontal casting and rolling, followed by grinding to remove distortions and polishing to give a clear, transparent but expensive product. The plate glass manufacturing process is now practically obsolete. It has been replaced by the float process.
FLOAT GLASS
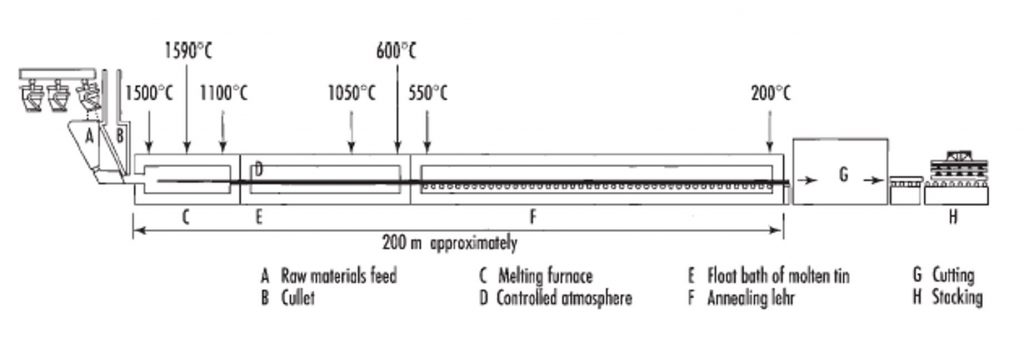
A furnace produces a continuous supply of molten glass at approximately 1100°C, which flows across the surface of a large shallow bath of molten tin contained within an atmosphere of hydrogen and nitrogen (this prevents oxidation of the surface of the molten metal). The glass ribbon moves across the molten metal, initially at a sufficiently high temperature for the irregularities on both surfaces to become evened out leaving a flat and parallel ribbon of glass.
The temperature of the glass is gradually reduced as it moves forward until, at the end of the molten tin, it is sufficiently solid at 600°C not to be distorted when supported on rollers. Thickness is controlled by the speed at which the glass is drawn from the bath. Any residual stresses are removed as the glass passes through the 200 m annealing lehr or furnace, leaving a fire-polished material. Then, the glass is washed, and substandard material is discarded for recycling. The computer-controlled cutting, firstly across the ribbon, then the removal of the edges, is followed by stacking, warehousing, and dispatch.
Float glass for the construction industry is made within the thickness range of 2–25 mm, although 0.5 mm is available for the electronics industry. Many surface-modified glasses are produced by incorporating metal ions into the glass within the float process. Body-tinted glass, which is of uniform colour, is manufactured by blending additional metal oxides into the standard melt.
NON-SHEET PRODUCTS
Glass fibres
Continuous filament
Continuous glass fibres are manufactured by constantly feeding molten glass from a furnace into a forehearth fitted with 1600 accurately manufactured holes. Molten glass is drawn through these holes, at a rate of several thousand metres per second. The fibres are as small as 9 microns in diameter. They pass over a size applicator and are gathered together as a bundle before to being wound up on a collet. The material may then be used as rovings, chopped strand, or woven strand mats for the production of glass-fibre reinforced materials such as GRP (glass-fibre reinforced polyester), GRC (glass-fibre reinforced cement), or GRG (glass-fibre reinforced gypsum).
Glass wool
Glass wool is used as an insulation material.
Cast glass
Glass may be cast and pressed into shape for glass blocks and extruded sections.
Profiled sections
Profile trough sections in clear or colored 6 or 7 mm cast glass are manufactured in sizes ranging from 232 to 498 mm wide, 41 and 60 mm deep, and up to 7 m long, with or without stainless steel longitudinal wires. The system can be used horizontally or vertically, as single or double glazing, and as a roofing system spanning up to 3 m.
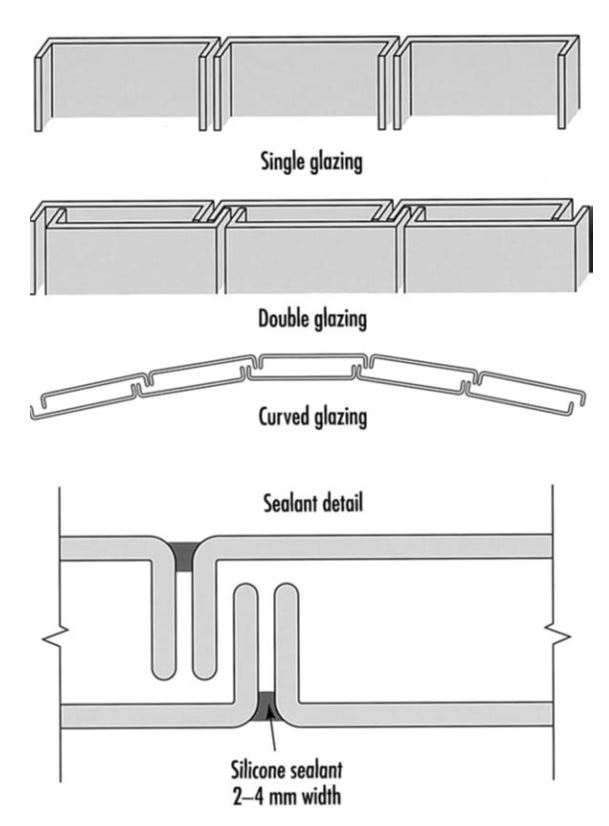
A large radius curve is possible as well as the normal straight butt jointed system. The joints are sealed with a one-part translucent silicone.
Amber or blue-tinted versions are available for solar control or aesthetic reasons. The double-glazed system produces a sound reduction within the 100–3200 Hz range of typically 40 dB.
The incorporation of 16-mm-thick translucent aerogel-insulated polycarbonate panels into profiled trough sections significantly increases the thermal insulating properties of the units. Airborne sound insulation is enhanced. Light transmission through the translucent aerogel panels is approximately 50%.
Glass blocks
Glass blocks for non-load-bearing walls and partitions are manufactured by casting two half blocks at 1050°C, joining them together at 800°C. The process is then followed by annealing at 560°C. The void space is partially evacuated. The standard blocks are 115, 190, 240, and 300 mm square with thicknesses of 80 and 100 mm, although rectangular and circular blocks are also available. The variety of patterns offering differing degrees of privacy includes clear, frosted, and crystal designs with colours from blue, green, and grey to pink and gold. For exterior and fire-retarding applications natural or coloured mortar (2 parts Portland cement, 1 part lime, 8 parts sand) is used for the jointing. Walls may be straight or curved. Bullet-proof blocks are available for higher security situations. For interior use, blocks can be laid with sealant rather than mortar.
Glass blocks jointed with mortar give a fire resistance of 30 or 60 minutes of stability and integrity. But, it will not give insulation. Fire stop blocks (F-30) are manufactured from 26 mm rather than 8 mm glass. It offers increased fire protection of two hours’ integrity and 30 minutes’ thermal insulation.
SHEET PRODUCTS
Standard float glass sizes
The standard thicknesses for float glass are 3, 4, 5, 6, 8, 10, 12, 15, 19, and 25 mm to maximum sheet sizes of 3 to 12 m. Thicker grades are available in smaller sheet sizes.
Traditional blown and drawn glasses
Traditional blown and drawn glasses are available commercially both clear and in a wide range of colours. Drawn glass up to 1600 – 1200 mm is optically clear but varies in thickness from 3 to 5 mm. It is normally used for conservation work where old glass requires replacement. The blown glass contains variable quantities of air bubbles. Also, it has significant variations in thickness giving an antique appearance.
Curved sheet glass
Curved glass can be manufactured by heating annealed glass to approximately 600°C when it softens and sag-bends to the shape of the supporting mould. Sheets up to 3 m – 4 m can be bent with curvature in either one or two directions. Bent glass can subsequently be sandblasted, toughened, or laminated, even incorporating coloured interlayers if required.
Self-cleaning glass
Self-cleaning glass has an invisible hard coating of 15 microns thick.
These coatings include two special features. The surface incorporating titanium dioxide is photocatalytic. It absorbs ultraviolet light, which with oxygen from the air breaks down or loosens any organic dirt on the surface.
Furthermore, the surface is hydrophilic. It causes rainwater to spread evenly over the surface, rather than running down in droplets. Therefore, the surface is uniformly washed and prevents any unsightly streaks or spots from appearing when the surface dries.
Self-cleaning glass has a somewhat greater mirror effect than ordinary float glass, with a faint blue tint. It is available as normal annealed glass and also in toughened or laminated form. The surface coating, which reduces the transmittance of the glass by about 5%, is tough but as with any glass can be damaged by scratching. A blue solar control version reduces the solar heat gain by approximately 60% depending upon the thickness of the glass used and its combination in a double-glazing system.
Clear white glass
Standard float glass is somewhat greener due to the effect of iron oxide impurities in the key raw material sand. However, clear white glass can be produced, at a greater cost, by using purified ingredients. The light transmittance of clear white glass is approximately 2% greater than standard glass for 4 and 6 mm glazing.
Embossed pattern glass
A wide range of 3, 4, 6, 8, and 10 mm patterned glass is commercially available. The degree of privacy afforded by the various glasses is not only dependent upon the pattern. It also depend upon the relative lighting levels on either side and the proximity of any object to the glass. Patterned glasses may be toughened, laminated, or incorporated into double-glazing units for thermal, acoustic, or safety considerations.
Screen printed glass
White or coloured ceramic frit is screen printed onto clear or tinted float glass. It is then toughened and heat soaked, causing the ceramic enamel to fuse permanently into the glass surface. Standard patterns or individual designs may be created, giving the required level of solar transmission and privacy.
Decorative etched and sandblasted glass
Acid etched glass, 4 mm and 6 mm in thickness, is available to a maximum sheet size of 2140 – 1320 mm with a small range of patterns. Etched glasses need to be handled carefully on-site, as oil, grease, and finger marks are difficult to remove completely. Similar visual effects can be achieved by sandblasting techniques, but it gives the surface finish less smooth. Patterns may be clear on a frosted background or the reverse, depending upon the aesthetic effect and level of privacy required.
Georgian wired glass
Georgian wired glass is produced by rolling a sandwich of a 13 mm electrically welded steel wire mesh between two ribbons of molten glass. This produces the standard cast 7 mm sheet, suitable when obscuration is required. Wired glass is not stronger than the equivalent thickness of annealed glass.
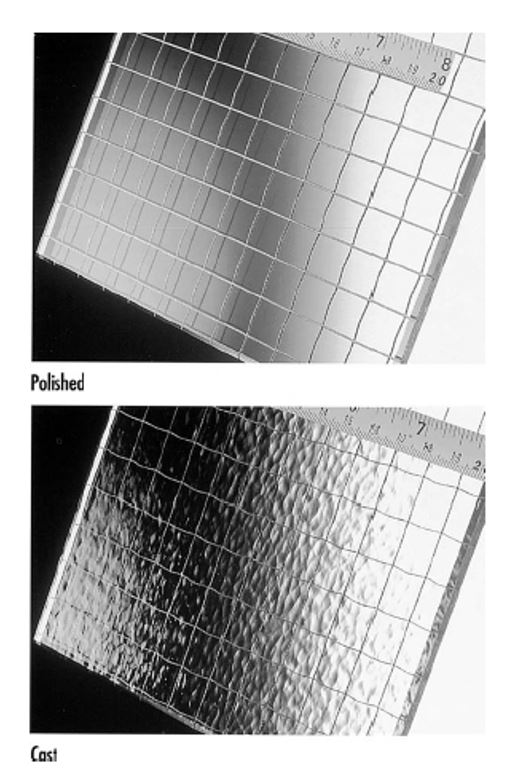
However, when cracked, the pieces remain held together. On exposure to fire, the wire mesh dissipates some heat. But, ultimately Georgian glass will crack, particularly if sprayed with water when hot. Accidental damage may cause the breakage of the glass. But again it is retained in position by the mesh, at least until the wires are affected by corrosion.
Toughened glass
Toughened glass is up to four or five times stronger than standard annealed glass of the same thickness. It is produced by subjecting preheated annealed glass at 650°C to rapid surface cooling by the application of jets of air. This causes the outer faces to be set in compression with balancing tension forces within the centre of the glass. As cracking within glass commences with tensile failure at the surface, much greater force can be withstood before this critical point is reached. Toughened glass cannot be cut or worked. Therefore all necessary cutting, drilling of holes, and grinding or polishing of edges must be completed in advance of the toughening process.
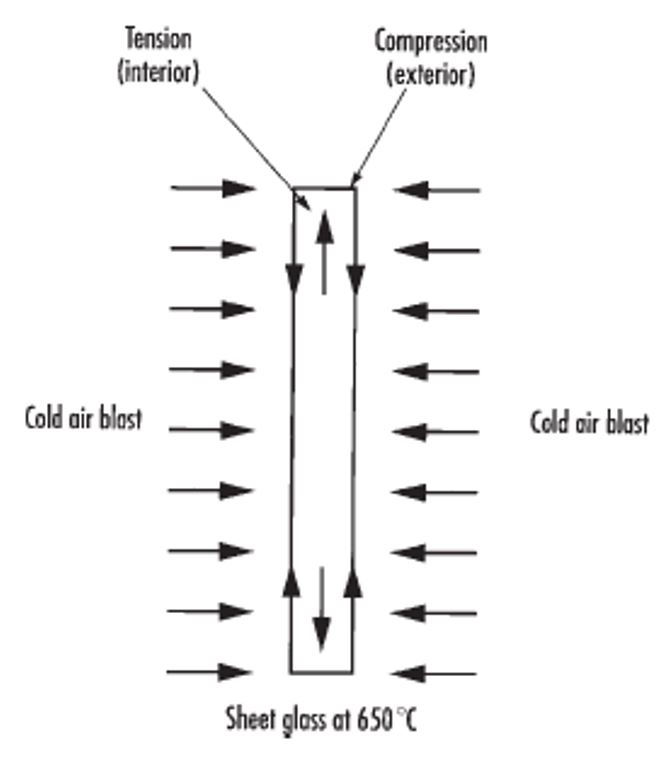
Toughened glass will withstand considerable extremes of temperature and sudden shock temperatures. When broken, it shatters into small granules. This is not likely to cause serious injuries related to the accidental breakage of annealed glass. Any standard float, coated, roughcast, and patterned glasses can be toughened.
Heat-strengthened glass
Heat-strengthened glass is manufactured by a similar process to toughening. But, it is done at a slower rate of cooling which produces only half the strength of toughened glass. On severe impact, heat-strengthened glass breaks into large pieces like annealed glass. Therefore it cannot be considered a safety glass. Heat-strengthened glass is frequently used in laminated glass where the residual strength after fracture gives some integrity to the laminate. Typical applications include locations where resistance to wind pressure is necessary, such as the upper storeys and corners of high buildings.
Laminated glass
Laminated glass is produced by bonding two or more layers of glass together with a plastic interlayer of polyvinyl butyral (PVB) sheet or a polymethyl methacrylate low-viscosity resin.
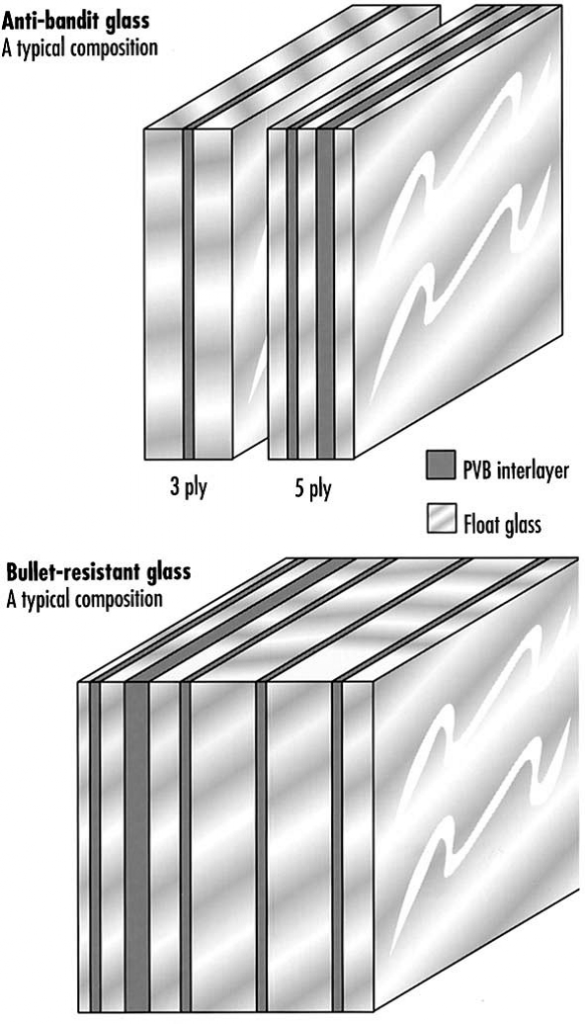
The lamination process increases the impact resistance compared to annealed glass of the same thickness. Furthermore on impact, whilst the glass laminations crack, they do so without splintering or disintegration, being held together by the interlayer. Therefore, laminated glass can be defined as safety glass. The impact resistance of laminated glass may be increased using thicker interlayers or increasing the number of laminates or the inclusion of polycarbonate sheets. Typically, anti-bandit glass has two or three glass laminates while, depending on the anticipated caliber and muzzle velocity,
bullet-resistant glass has four or more glass laminates. To prevent spalling, the rear face of bullet-resistant glass may be sealed with a scratch-resistant polyester film.
Insulating glass
Insulating glasses are manufactured from float glass laminated with either intumescent or gel materials. Intumescent laminated glass has clear interlayers. When exposed to fire, intumescent or gel materials expand to a white opaque material. It prevents the passage of conductive and radiant heat. The glass layers adjacent to the fire crack but retain integrity owing to their adhesion with the interlayers. The fire resistance, ranging between 30 and 120 minutes for insulation and integrity, depends on the number of laminations, usually between 3 and 5.
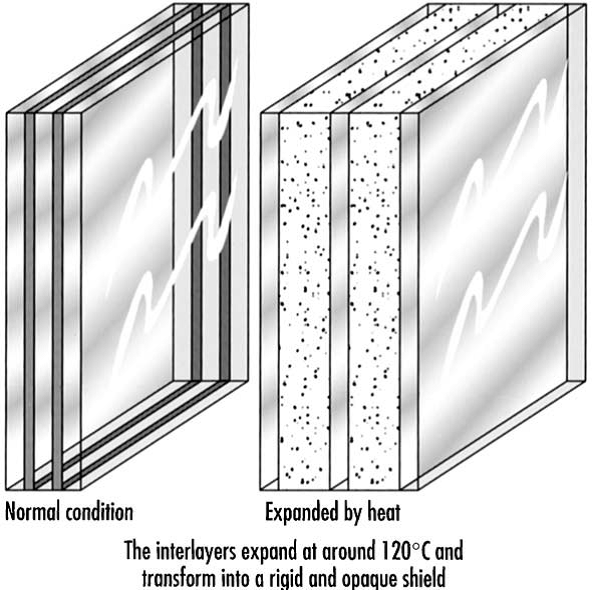
Fire-resistant glass with intumescent material laminates
SPECIAL GLASSES
One-way observation glass
Where unobserved surveillance is required, one-way observation mirror glass can be installed. To maintain privacy, the observer must be at an illumination level no greater than one-seventh that of the observed area. Also, he should wear dark clothing. From the observed area, the one-way observation glass has the appearance of a normal mirror. One-way observation glass is available in annealed, toughened, or laminated.
Mirror glass
Standard mirror glass is manufactured by the chemical deposition onto float glass of a thin film of silver, from aqueous silver and copper salt solutions. The film is then protected with two coats of paint or a plastic layer. Mirror glass is produced by the online application of a three-layer coating of silicon-silica-silicon, which acts by optical interference to give the mirror effect.
Alarm glass
Glass containing either a ceramic loop or a series of straight wires can be incorporated into an intruder alarm system. It is set to activate when the glass is broken. Usually, straight-wired alarm glass is incorporated into a laminated system, while a ceramic loop circuit would be fixed to the inner face of the toughened outer pane within a double-glazing system.
Electrically-heatable laminated safety glass
It incorporates fine electrically conducting wires which may be switched on when there is a risk of condensation. Typical applications are in areas of high humidity, such as swimming pools, kitchens, and glass roofs, particularly when there are significant differences between the internal and external temperatures.
Electromagnetic radiation-shielding glass
Itcan be used to protect building zones containing magnetically stored data from accidental or deliberate corruption by external electric fields. For maximum security, the conducting laminates within the composite glass should be in full peripheral electrical contact with the metal window frames and the surrounding wall surface screening.
X-ray protection glass
It contains 70% lead oxide, which produces significant shielding against ionizing radiation. The glass is amber in colour due to the high lead content. A 6 mm sheet of this lead glass has the equivalent shielding effect of a 2 mm lead sheet against radiation.
Variable transmission (smart) glasses
Variable transmission or smart glasses change their optical and thermal characteristics under the influence of light (photochromic), heat (thermochromic), or electric potential (electrochromic). These glasses offer the potential of highly responsive dynamic climate control to building facades. These smart materials including thermotropic products are also available as plastic laminates for incorporation into laminated glass systems.
Electro-optic laminates
Electrically operated vision-control glass consists of a laminated system of glass and polyvinyl butyral layers containing a polymer-dispersed liquid crystal layer, which can be electrically switched from transparent to white/translucent for privacy.
Intelligent glass
Conventional glass coatings reduce both light and heat transmission. However, a coating based on tungsten-modified vanadium dioxide allows visible light through at all times but reflects infrared radiation at temperatures above 29°C. Thus, at this temperature, further heat penetration through the glass is blocked. Therefore the intelligent glass, which has a slight yellow/green colour, admits useful solar gain in cooler conditions but cuts out excessive infrared solar gain under hot conditions.
Intelligent glass facades
An intelligent glass building facade changes its physical properties, in response to sensors detecting the external light and weather conditions. It results in reducing the energy consumption necessary to maintain the appropriate internal environment. Therefore intelligent facades have ecological significance in reducing global greenhouse emissions. It also reduces the operational building costs to clients and users.
STRUCTURAL GLASS
Glass columns are frequently used as fins to restrain excessive deflection caused by wind and other lateral loads to glass facades. The fixings between the façade glazing and fin units are usually stainless steel clamps bolted through preformed holes in the toughened or laminated glass, although silicone adhesives can also be used. A soft interlayer between the metal fixing and the glass is incorporated to prevent stress concentrations on the glass surface and to allow for differential thermal movement between the glass and metal. Glass is strong in compression and therefore an appropriate material for load-bearing columns and walls, providing that the design ensures sufficient strength, stiffness, and stability.